فرآیند ریخته گری
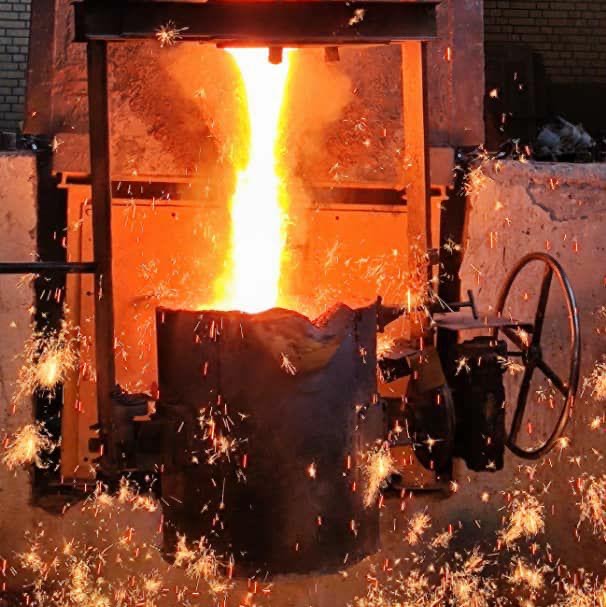
ریخته گری:
ریخته گری یکی از روش های شکل دادن قطعات فلزی است که شامل تهیه مذاب از مورد نظر و ریختن آن در محفظهای به نام قالب است به گونهای که پس از انجماد مذاب شکل و اندازه و خواص مورد نظر تامین شود. به صورت کلی ریخته گری را باید مجموعهای از عملیات ذوب تهیه قالب و ریختن مذاب دانست. ریخته گری روشهای مختلفی دارد که عوامل زیادی در انتخاب فرآیند نقش دارند. هدف از تولید قطعات مهندسی دو چیز است: 1- قطعه با شکل مشخص 2- قطعه با خواص متالورزیکی معین
ماده اولیه معمولا نه شکل معین و مورد نظر را دارد و نه خواص. این دو هدف طی فرآیند تامین میشوند بدین منظور دو راه وجود دارد: 1- شکل دهی در حالت مذاب 2- شکل دادن در حالت جامد (فرزکاری، ماشین کاری و فورج نورد)
مزایای روش ریخته گری:
1- قابلیت تولید قطعات بسیار کوچک و بسیار بزرگ (در اکثر روشهای دیگر محدودیت اندازه قطعه وجود دارد.)
2- امکان تولید قطعات پیچیده
3- تولید قطعات به صورت یکپارچه
4- امکان تولید الیاژهای خاص (چدن ها)
چدن کاربرد زیادی در صنعت دارد. در چدن به علت بالا بودن درصد کربن، گرافیت آزاد در ساختار وجود دارد، در نتیجه تغییر شکل پلاستیک نخواهد داشت، تنها راه تولید قطعات چدنی ریختهگری است در نقطه یوتکتیک وقتی انجماد صورت میگیرد بیش از 2 درصد کربن نمیتواند حل شود و بهصورت آزاد ایجاد میشود که قابلیت تغییر فرم ندارد.
محدودیت های روش ریخته گری
1- قالبی باید تهیه شود که قابلیت تحمل حرارت فلز مذاب را داشته باشد، به خصوص برای آلیاژهاییکه دارای نقطه ذوب بالایی هستند. در این مورد از مواد دیرگداز برای ساخت قالب استفاده میکنیم.
2- چون در روش ریخته گری عملیات ذوب و انجماد وجود دارد امکان تشکیل حفره های انقباضیوجود دارد که اثرات منفی روی خواص دارد.حین انجماد امکان جدایش وجود دارد. (بیشتر مربوط به قطعات بزرگ میباشد.) فاز اولیه جامد عنصر الیاژی کمتری دارد یعنی انجماد از جایی شروع میشود که دمای کمتری دارد(دیواره قالب) در این محل فاز جامد وجود دارد در نتیجه علی رغم همگن بودن مذاب جامد تشکیل شده در دیوارهترکیب متفاوتی از بقیه مذاب دارد و با گذشت زمان و انجماد عناصر الیازی پس زده میشود. دراخرین نقطه انجماد که مرکز قالب میباشد غلظت عنصر الیازی زیاد خواهد بود پس جدایش اتفاقافتاده و قطعه همگن نخواهد بود.
روشهای ریخته گری:
انتخاب روش به نوع آلیاژ، تعداد قطعات، مشخصات مورد انتظار از قطعه است.
1-ریخته گری در قالب های دائمی:
بعد از انجماد، قالب باز میشود و قالب تخریب نمیشود و امکان استفاده مجدد و ورود دوباره مذابوجود دارد، با یک قالب میتوانیم چندین قطعه تولید کنیم یعنی سرعت کار زیاد و هزینه کنم است.
2-ریخته گری در قالب های موقت:
بعد از انجماد، قالب شکسته میشود تا بتوان به راحتی قطعه را از آن خارج کرد، در این روش برایهر قطعه یه قالب لازم داریم.(قالب های ماسه ای و سرامیکی)
ریخته گری در قالب های دائمی
1-ثقلی
2-تحت فشار بالا
3-تحت فشار کم
ریخته گری ثقلی:
عامل وزن موجب ورود مذاب به قالب میشود، در قالب رو باز، مذاب به جز سطح بالایی که با هوادر تماس است با سطح فلز ماشین کاری شده در تماس بوده و در نتیجه قسمت بالایی امکان اکسیداسیون وجود دارد. همچنین کیفیت سطح بالایی بر خلاف قسمت های کناری و کف قطعه خوب نیست؛ به همین دلیل برای تولید قطعات صنعتی از قالب روباز استفاده نمیشود.در قالبهای بسته مذاب در همه جا با سطح فلز در تماس است. در قالبهای بسته به منظور ورود مذاب به داخل سیستم راهگاهی طراحی میشود.در این حالت قطعه کیفیت خوبی ندارد چون ریختن مذاب از بالا به کف قالب باعثمیشود هوایی که قبلا در قالب بوده حبس شده و ایجاد اخال کند. تمامی قطعات صنعتی مثل پیستون خودرو از روش ریختهگری ثقلی تولید میشود.
ریخته گری تحت فشار بالا:
در این روش مذاب داخل سیلندر تزریق، ریخته میشود ( به اندازه حجم قطعه مورد نظر) پیستون به سرعت فلز مذاب را داخل قالب فرو میکند و نیرو تا پایان انجماد اعمال خواهد شد، عامل پر شدن قالب در این روش فشار اعمالی توسط پیستون تزریق است. در ریختهگری ثقلی، فشار مذاب وابستهبه وزن است، اما در این روش فشار مذاب در همه جا برابر فشار اعمالی توسط پیستون میباشد.
ریخته گری تحت فشار کم:
برای انتقال فلز مذاب به قالب از فشار خیلی کمتر از فشار بالا استفاده میشود، در فشار زیاد چون. پاشش وجود دارد، احتمال اکسیداسیون زیاد است اما چون زمان کم است، ناچیز میباشد.
ریخته گری در قالبهای موقت
1- قالب موقت/ مدل دائمی
2- قالب موقت/مدل موقت
قالب موقت/ مدل موقت همان ریختهگری دقیق است که کیفیت سطحی با لایی دارد و در این نوع ریختهگری دقت ابعادی بسیار بالا میباشد، آلیاژهای استحکام بالا، طلا و جواهرات، لوازم جراحی وپرههای توربین با این روش ریختهگری می شوند. قالبهای موقت عمدتا از جنس نسوز هستند و قابلیت پلاستیستیه را با اضافه کردن سایر موارد به وجود میآید.
اجزای مختلف قالب ماسهای: ماده دیرگداز، چسب، کاتالیست.
:روش های قالبگیری:
1) روش دستی
2) روش ماشینی
روش دستی: در این روش کلیه مراحل قالب گیری توسط نیروی انسانی و با دست انجام می پذیرد.
روش ماشینی:
1) ضربهای / فشاری
2) فشار بالا
3) انفجاری
4) فشار هوا
5) دیزاماتیک